Making the sgian
From a piece of tanned hide to a simple yet elegant sheath. A dull block of rough timber to a polished mirror of finest grain. And a cold lump of rock to a shining pommel of golden flames. Our aim at Dalriada Sgian Dubhs is to awaken the sleeping beauty and natural qualities of the resources around us. Our woods, leathers, antlers, agates and metals already have the qualities we need of them; they just have to be allowed to shine. And so in his workshop Christopher sands, shapes and polishes the materials he sources until they come together to form sgians worthy of our shared heritage.
The results are sgians crafted by hand, with care, and with an attention to detail that makes each piece unique and never to be repeated.



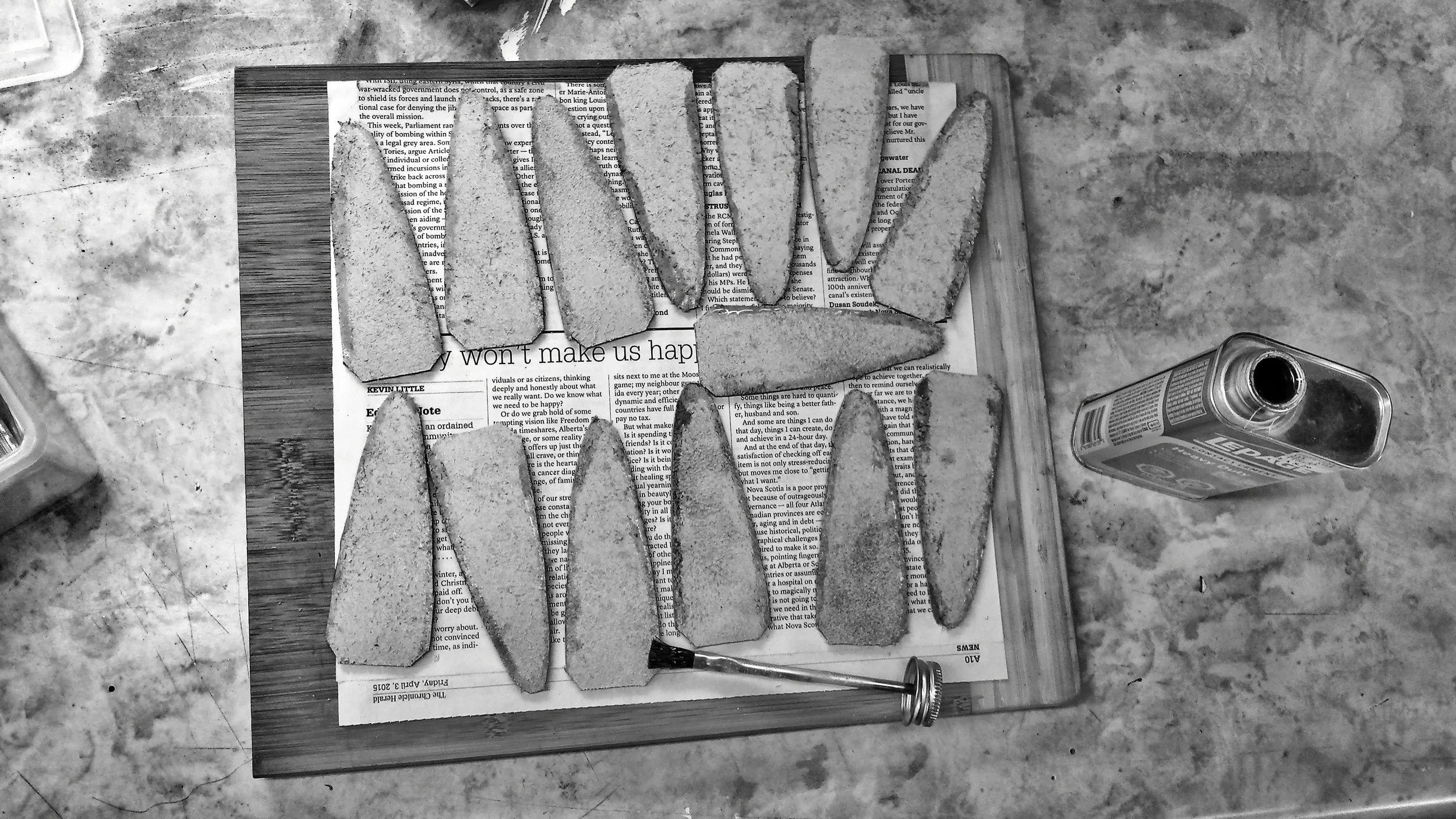

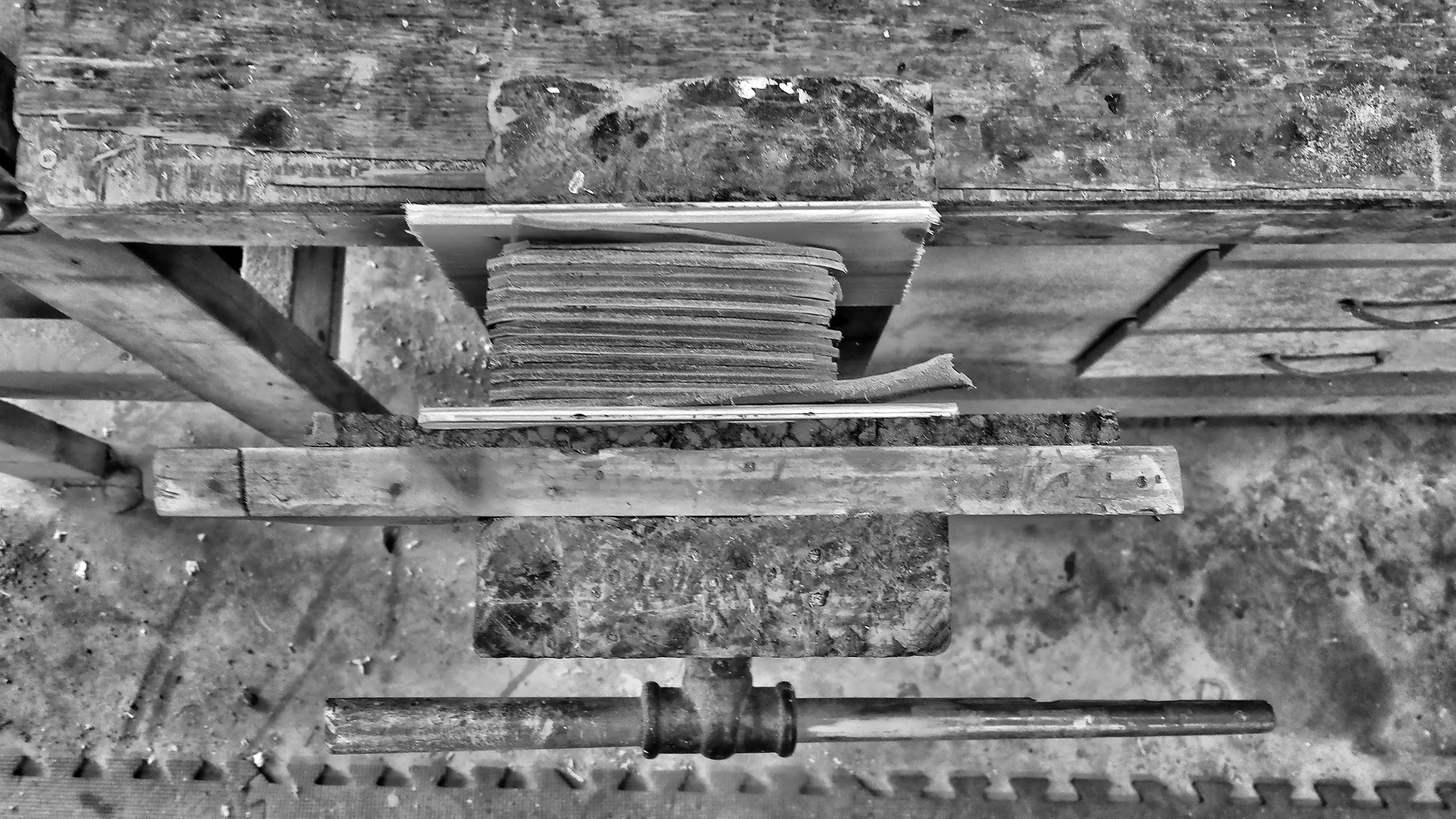
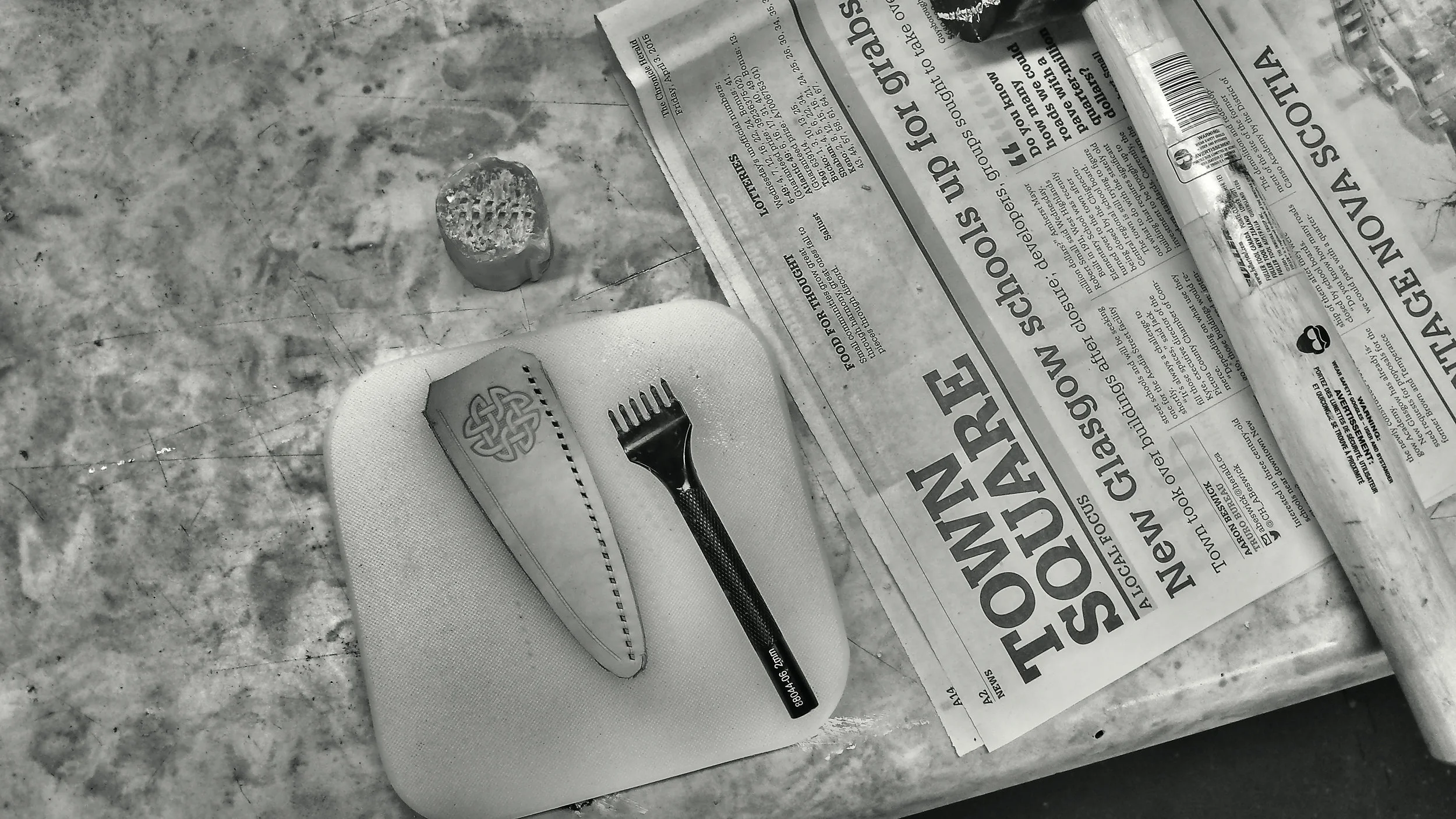







it starts with the sheath...
It starts with the one piece of the sgian that is hidden behind the sock, the sheath. However, just because others won’t see it doesn't mean it shouldn't be given the same time and care that we give to the parts we can see. We start with vegetable tanned hide that we cut into the basic shape of the sheath before stamping a variety of Celtic patterns onto the face side. From there we glue and stitch the sheaths before dyeing them to either of our black or antique brown finishes. We bevel the edges, burnish them to make a smooth finish and then apply a final coating to finish the edge. All that is left is a quick buff and light wax to ensure a elegant and simple sheath that enhances the sgian it holds.
Selecting the elements...
Historically sgian dubhs were thought to have been made with hardened bog oak and stag horns collected from the hills and glens of the Scottish Highlands. Later as these sgians became decorative and worn for display they began to be made from rare woods like ebony and adorned with silver fittings and quartz pommels.
Dalriada Sgian Dubhs continues this harmony between locally sourced materials in the form of figured maples and moose antlers with the luxury of rare flame agates and sterling silver fixings. Although we attempt to source all of our materials from as close to our workshop as possible we also integrate exotic materials in the form of ebony accents that pay homage to some of the great sgians of the past as well as rare walnuts, oaks and maples sourced from craftsmen in California who reserve their finest pieces for our sgians.
The results are stylish, elegant, and honest sgians, which are connected to the history, culture, and landscapes that forged them.
Shaping the Sgian...
Once the materials have been sourced and the basic shapes formed, the next task is shaping the handle with teeth and with grit to get down to the final design. Christopher doesn't work from templates for his sgian's designs and instead allows the sgian and the materials to direct the final form. This allows details to take priority and ensures that each sgian is as unique as the next.
The final stage in making the sgian is the final polish. This is the stage where the grain of the wood is finally revealed in all its glory and begins with a light layer of pure tung oil, a natural nut oil that enhances the detail and depth of the wood's figuring without applying artificial artefacts. From there a variety of pastes, gradually polish the handles to a mirror finish and a final wax seals and protects the handles from the rigours of a wild ceilidh or strenuous highland games.
What are left are one of kind sgians that reveal the true beauty of our landscapes and continue the heritage that began in the glens of Scotland.